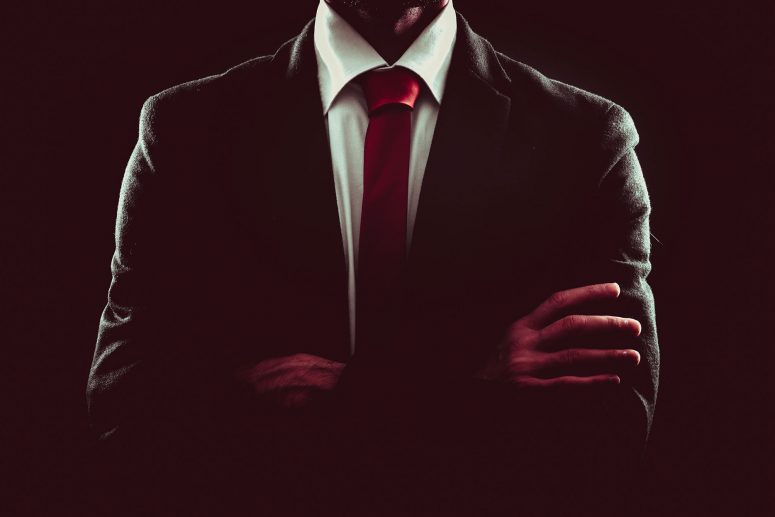
Erosion and corrosion in pipeline design
Posted on March 5, 2022
1.0 Purpose:
This note provides information and guidance about erosion, erosion-corrosion and flow accelerated corrosion in pipelines and piping. It discusses mechanisms and applicable scenarios and that a hydraulics engineer needs to be aware of, at the design stage. The focus of this note is on oil and gas pipelines, though the principles would be equally applicable to in-plant piping. When performing hydraulic calculations, it is quite common to see young engineers restrict their calculations to considerations of allowable velocities and pressure drops. This oversimplification of the line-sizing design process ignores many relevant aspects, some of which are related to pipeline and piping integrity. In the Hydrocarbon industry, we deal with many hazardous fluids and the hydraulics design process must incorporate a detailed study of all relevant issues that have a bearing on functionality and safety. Corrosion and erosion
phenomena have a bearing on material selection, design life and safety of piping and pipeline systems.
2.0 Key concepts:
Erosion can be defined as mechanical loss of material by the impact of liquid droplets and/or solid particles in flowing environments. Erosion becomes a problem when pipeline operating conditions lead to erosion, with consequent damage to equipment, or if production is constrained due to erosion velocity limits. Erosion-corrosion refers to increase in corrosion rates caused by erosion of a protective layer (oxide, carbonate, sulphide) by erosive liquid flow. The metal then reacts to grow a new layer via corrosion, which is removed again , the process being repeated as long as fluid conditions allow. So, erosion-corrosion has little to do with erosion of the metal itself. Erosion-corrosion is defined as “degradation of material caused by both mechanical and chemical processes”. Flow accelerated corrosion (FAC) is a similar type of corrosion phenomenon, in which the normally protective Oxide layer on Carbon-Steel and Low Alloy Steel dissolves in flowing water. The underlying metal corrodes to re-create the Oxide and thus the metal loss continues. FAC is different from erosion-corrosion, as there is no mechanical impact of particle, bubbles or cavitation that removes the oxide layer. Rather, the protective Oxide layer dissolves due to water chemistry/electrochemistry and mass transfer effects (flow velocity). In many cases, a combination of erosion corrosion and FAC could be prevalent. Typically, chemical industry/power plants are familiar with FAC in wet steam and hot steam condensate lines.
Erosion and Erosion-Corrosion in Oil and Gas Processing Systems
Typical scenarios which can result in increased erosion threat to Oil and Gas pipeline systems are:
• Increased water-cuts causing increasing fluid volumes to be pushed through, to maintain oil production.
• Increased use of multi-phase flow in the transport of production fluids.
• Increased sand and solids production rates due to a number of factors, such as increased water-cut, use of proppant and reservoir fracturing techniques.
The four main mechanisms by which produced fluids cause erosion are:
• Erosion by non-corrosive fluids through liquid droplet impact.
• “Pure” solids erosion by a non-corrosive fluid carrying solid particles.
• Erosion-corrosion by a corrosive medium in the absence of solids.
• Erosion-corrosion by a corrosive medium containing solids.
For pure single phase non-corrosive gases, in the total absence of solids or entrained liquids, there are no velocity limits to avoid erosion. However, there are other flow related phenomena that need to be considered for high velocities, e.g., noise, vibration and static electricity. Similarly, for single phase non-corrosive liquid flow (i.e. totally solids free and with no entrained gas bubbles), there are no velocity limits to avoid erosion damage. However, velocity limitations arise due to others causes such as vibration, surge and cavitation. It needs to be emphasized that even very low levels of solids can cause significant erosion,
hence “solids free” means that there is absolutely no possibility of solid particles being transported in the flowstream. Liquid droplet erosion (e.g., in annular mist flow) of metals under non-corrosive conditions in
the total absence of solids will only be a concern at velocities above 70 m/s. This is the maximum velocity limit defined to avoid the possibility of droplet erosion for gas condensate wells. Thus, for an ideal case of solids free environment, the only erosion damage mechanisms would be due liquid impingement or gas bubble impingement (in multiphase flow). However, such an ideal case of solids free flow is uncommon in practice. In the case of multiphase flow of corrosive fluids, when solids are absent, erosive effects can
be produced by the flow regime physically damaging protective corrosion-product layers. Of course, in corrosive environments, corrosion will occur even below the erosion velocity of corrosion product layers. The situation is exacerbated if the flow rate is high enough to cause the mechanical breakdown of the protective corrosion product layer. For example, in environments containing CO2 or O2, corrosion is often controlled by the presence of protective layers. In the case of Carbon Steel, this is normally a layer of precipitated layer of corrosion product; in the case of Duplex and Austenitic Stainless Steels, it will be a very thin (around 10- 9 m or 10 0A) passive layer; in the case of 13 % Cr steel, it will be something intermediate between a passive layer and a passive film. Under solids-free conditions, these protective layers can be damaged or eroded by pure fluid flow. Droplet impact in multi-phase flow is possible (e.g., annular mist flow) and the resultant damage can be significantly more severe than the damage caused by shear stress forces in pure liquid flow. Passive films on materials such as Duplex Stainless Steel are the strongest and most adherent and reform very rapidly; precipitated films on Carbon Steel are the weakest and least adherent and reform relatively slowly. Damage, if it occurs, is most likely at bends and elbows between the 15 0 and 50 0 positions on the outer radius. The rate of attack is uncertain. For Carbon Steel, the localized damage of any protective layers is liable to initiate a form of ‘mesa’ attack (steep-sided pitting in CO2 service) and the rate of penetration could be upto twice the bare-surface corrosion rate. For 13% Cr steel, localized pitting may result, and under such circumstances, the ability of the alloy to repair damage to the protective film will be critical. There could be significant delay in reformation of the protective film on 13% Cr material at lower temperatures (below say 80 0C). However, it has been found that above this temperature, film repair can be very rapid in CO2 service. For duplex stainless steel, the protective film (passive layer) is very resilient, even if it is damaged, it reforms (re-passivates) very rapidly. Therefore, little or no interaction between erosion and corrosion would be expected for duplex stainless steel.
Erosion velocity calculations
Different velocity limits will apply in different situations, depending on the flow (gas, liquid or multi-phase gas/ liquid).
Solids-free flow
For the specific case of pipes carrying solids free corrosive (wet) gas or multi-phase flows, theC factor method specified in API 14E [Ref.1] should be used to etermine erosion velocity limits. These criteria apply to nominally sand-free conditions, defined as sand content less than 1 pptb for liquid / multiphase systems or up to 0.1 lb/mmscf for gas systems. The “C” factor method imposes velocity limits such that enhanced corrosion due to removal of naturally occurring corrosion products is avoided.
For example, suggested values of “C” factor for solids free conditions are 135, 300 and 350 ft/s(lb/ft3) 0.5, for Carbon Steel, 13% Cr and Duplex stainless steels espectively, under conditions of CO2 corrosion, for multi-phase flow.
For fluids which contain sand, the C factor method is not recommended and erosion rates should be calculated using erosion rate models Fluids containing solids The presence of solids can lead to erosion that damages or removes protective layers as well as cause physical removal of metal. Erosion rates are proportional to the solids concentration in the fluid.
It is unclear whether there is a threshold solids concentration below which erosion cannot occur.
However, 1 pound of solids per thousand barrels (1 pptb) for oil /multiphase systems or 0.1 pounds of solids per million standard cubic feet of gas (0.1 lb/mmscf) for gas systems, is the limit of the level of detection of current sand monitoring techniques and hence suggested here as a guideline to decide whether fluids are ‘nominally sand free’.
This is different from ‘totally sand free’ which indicates service where there is absolutely no risk of entrained solids in the flowstream. Erosion depends critically on the fluid flow regime. Solid particles carried in gas flow may hit pipe walls at the full gas velocity, although it is likely that in many cases the solid particles will drop out of the gas stream and either form a static bed or a moving bed (moving dunes, scouring). Under full liquid flow, solid particles will frequently travel at the liquid velocity, but will be significantly slowed by a liquid barrier layer on the pipe wall before striking the pipe material surface. Under multi-phase flow, some solid particles may be carried at/near the gas velocity (if the flow is annular mist) and may or may not be slowed down by a liquid barrier layer, depending on the thickness of the annular liquid film. For non-corrosive fluids containing sand, the basic erosion mechanism of most metals is ductile ploughing of the surface by impacting solid particles. The material lost per impact is greatest at angles of impact between 150 and 600 and is proportional to m× (Vi)n , where n is between 2
and 2.5, m is the particle mass and Vi the actual particle impact velocity. The overall wastage rate is then the mass loss per impact times the impact rate. In the simplest case, the rate of
impact is equal to the mass flow rate of the particles divided by the mass per particle and if it is assumed that the area of impact is the projection of the cross-sectional area onto a bend (or a projected area in the path of the flow, such as a restriction) then the overall wastage rate per unit area (i.e the penetration rate) will be a function of m(Vi)n times M/m divided by the pipe cross-sectional area A, where M is the solids production rate. However, M will be proportional to the product of the solids concentration S and the mixed fluid velocity, V. Thus the erosion rate formula can be expressed as:
E = K × m× (Vi) n × M/ (m×A)
Or
E= K’× (Vi) n × S× V/d2
Where d is the pipe diameter, K and K’ are constants and E is the erosion rate.
This can be further simplified by assuming that the particle impact velocity Vi equals the mixed fluid velocity, V (or is a constant proportion of the mixed fluid velocity) and n=2, so that:
E = K’ × (Vi)2× M/ d2
Or
E= K’× (Vi) 3×S/d2
Units are as below:
E is the erosion rate in mm per year (we normally limit this to 0.1 mm per year)
V is the mixed velocity in m/s
d is pipe diameter in mm
M is sand production in g/s
While the above approach would suffice for most hydraulic calculations, more sophisticated commercial models are available as software packages and should be used if accurate estimates of erosion rates are required.
Flow Accelerated Corrosion (FAC)
FAC is commonly encountered in aqueous systems and involves aqueous electrochemistry as well as mass transfer effects. The mechanism of material loss involves the following steps:
• Electro-chemical formation of a corrosion layer
• Hydraulic damage to the corrosion layer
• Removal of the protective corrosion products due to high flow velocity
While flow velocities and pH are important in control of FAC, the following points are noteworthy:
• FAC sensitivity will increase in regions where due to internal separation e.g., in bends,
downstream of orifices, pipe entries, partially opened valves and in tee’s) the velocities
are higher than the plug-flow values. Liquid jet impact zones (e.g., impingement plates,
dividing tees, etc.) will be FAC sensitive regions as the boundary layer in these points will be thin at the beginning of the development zones.
• Increased levels of turbulence will amplify the problem even further. These zones typically occur in the above-mentioned areas and downstream of weld imperfections, thermowells and other inserts in the piping. In the turbulent boundary layer, mass transfer not only occurs by molecular diffusion, but is enhanced by turbulent convection.
In summary therefore, please be aware of the above material loss phenomena caused by erosion, erosion-corrosion and FAC, during hydraulic design of pipeline and piping systems.
3.0 References:
[1] Recommended Practice for Design and Installation of Offshore Products Platform Piping Systems, Fifth Edition, October 1991, Reaffirmed March 2020.